Auf einen Blick
- Aufgaben: Lead the Maintenance and Utilities team to ensure smooth operations in a high-tech manufacturing facility.
- Arbeitgeber: Join Thermo Fisher Scientific, a leader in R&D with over $40 billion in revenue.
- Mitarbeitervorteile: Enjoy a standard work schedule, collaborative culture, and opportunities for professional growth.
- Warum dieser Job: Make a significant impact in biotech while working in a cutting-edge environment focused on human health.
- Gewünschte Qualifikationen: Bachelor’s degree in Engineering and 7-10 years of maintenance management experience required.
- Andere Informationen: Experience with CMMS and GMP standards is a plus; strong leadership skills are essential.
Das voraussichtliche Gehalt liegt zwischen 48000 - 84000 € pro Jahr.
Work Schedule
Standard (Mon-Fri)
Environmental Conditions
Office
Job Description
Position Purpose
When you join us at Thermo Fisher Scientific, you’ll be part of an inquisitive team that shares your passion for exploration and discovery. With revenues of more than $40 billion and the largest investment in R&D in the industry, we give our people the resources and chances to create significant contributions to the world.
The Manager, Maintenance and Utilities is responsible for ensuring the efficient and compliant operation of all mechanical systems and non-electrical energy systems, such as boilers and clean steam, within the Lengnau facility. This role is critical to maintaining the high-tech, fully automated stainless steel GMP manufacturing facility dedicated to large-scale monoclonal antibody (MAB) production for human use. Within the responsibility of this role is also the day-to-day operations 24/7 of the GMP and Non-GMP Utility systems.
Position Responsibilities & Accountabilities
- Manage Daily Operations: Be responsible for the day-to-day activities of the Maintenance and Utilities Team, ensuring smooth and efficient operations.
- Team Leadership and Management: Lead, mentor, and develop the maintenance team to foster a high-performance culture. Provide clear direction, set performance expectations, and conduct regular performance evaluations. Foster a collaborative and inclusive work environment that encourages team members to share ideas and contribute to continuous improvement initiatives. Ensure the team is adequately trained and equipped to perform their duties safely and effectively.
- Assign tasks, inspect work, review documentation, and develop training programs.
- Regulatory Compliance & Statutory Inspections: Ensure all mechanical systems and non-electrical energy systems follow relevant health, safety, and environmental regulations, including GMP standards for the manufacturing of monoclonal antibodies (MABs) for human use. Be responsible for statutory inspections across all production areas, including cleanrooms and energy plants. Collaborate closely with quality assurance and legal teams to meet compliance standards and prepare for audits by regulatory bodies such as the FDA, EMA, and Swissmedic.
- CMMS Management: Use the site’s implemented Computerized Maintenance Management System (CMMS), One Maximo, to supervise and manage maintenance activities, ensuring transparency and efficiency. Be responsible for the scheduling and execution of maintenance tasks to ensure optimal equipment reliability and minimal downtime.
- Planned Preventative & Predictive Maintenance: Develop and implement a Planned Preventative Maintenance (PPM) program tailored to the high-tech, fully automated stainless steel GMP manufacturing facility. Use predictive maintenance technologies to supervise equipment conditions, ensuring the reliability of critical systems such as boilers and clean steam generators.
- Mechanical Systems and Non-Electrical Energy Infrastructure: Lead the maintenance of all mechanical systems, including large-scale stainless-steel reactors (12K L), boilers, and clean steam systems. Ensure the mechanical systems and non-electrical energy systems are maintained to support uninterrupted GMP manufacturing operations.
- Perform Additional Duties: Carry out additional responsibilities as assigned to support the overall success of the facility.
Quality
- Adheres to general cGMP rules, Quality policies, procedures and instruction as rolled out by the Quality function and endorsed by the site management (Deviations, CAPAs, Change Control, etc.).
- Actively contributes to continuous quality improvement initiatives and deviation reporting and follow-up.
- Represent the department as SME for the responsible area in audits and regulatory inspections.
EHSS
- Adheres to general safety rules, policies, procedures and instructions as rolled out by the EHSS functions and endorsed by the site management.
- Actively contributes to safety initiatives and issues as well as near miss reporting and follow-up.
Values & Behaviour
- Maintains commitment to Thermo Fisher Scientific values and alignment to ethics and legal compliance standards.
- Takes personal accountability for their presence, performance, and productivity for the achievements of defined objectives.
- Thinks and acts with a customer-centric attitude.
- Is intellectually curious and embraces Practical Process Improvement (PPI).
Position Qualifications
Education
- Bachelor’s degree in Engineering, Mechanical Engineering, Process Engineering, or a related field (or equivalent experience).
Experience & Competences
- Minimum of 7-10 years of experience in maintenance management, preferably in a high-tech, automated GMP manufacturing facility.
- Demonstrated experience in managing mechanical systems and non-electrical energy systems, such as boilers and clean steam.
- Proven track record of leading and developing high-performance maintenance teams.
- In-depth knowledge of GMP standards in manufacturing settings, particularly for human-use MAB production is an advantage.
- Strong understanding of GMP standards and maintenance requirements (NIST/USP/ISO).
- Experience managing cross-disciplinary teams and maintaining complex, highly regulated environments.
- Strong understanding of relevant regulatory frameworks (e.g., GMP, health and safety, environmental standards).
- Proven experience in using CMMS, particularly One Maximo, to manage maintenance operations across large, diverse facilities.
Additional Requirements
- Experience in managing maintenance and mechanical systems in a high-tech, automated manufacturing facility.
- Lead with an open attitude passionate about efficient problem solving.
- Strong project management skills and the ability to lead multiple concurrent projects.
- Excellent communication and interpersonal skills, with the ability to collaborate effectively with multi-functional teams.
- Participation in quality improvement initiatives and deviation reporting.
- Analytical and concept-based thinking and acting.
- Six-sigma, process improvement or related experiences are and advantage
#J-18808-Ljbffr
Manager, Maintenance and Utilities Arbeitgeber: Thermo Fisher Scientific Inc.
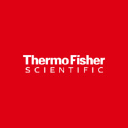
Kontaktperson:
Thermo Fisher Scientific Inc. HR Team
StudySmarter Bewerbungstipps 🤫
So bekommst du den Job: Manager, Maintenance and Utilities
✨Tip Number 1
Familiarize yourself with the specific mechanical systems and non-electrical energy systems mentioned in the job description, such as boilers and clean steam systems. Understanding these technologies will help you demonstrate your expertise during interviews.
✨Tip Number 2
Highlight your experience in managing maintenance teams and fostering a high-performance culture. Be prepared to share examples of how you've successfully led teams in previous roles, as this is a key responsibility for the position.
✨Tip Number 3
Research GMP standards and regulatory compliance relevant to monoclonal antibody production. Being knowledgeable about these regulations will show your commitment to quality and safety, which is crucial for this role.
✨Tip Number 4
If you have experience with CMMS, particularly One Maximo, be ready to discuss how you've utilized it to improve maintenance operations. This will demonstrate your technical skills and ability to manage complex systems effectively.
Diese Fähigkeiten machen dich zur top Bewerber*in für die Stelle: Manager, Maintenance and Utilities
Tipps für deine Bewerbung 🫡
Tailor Your Resume: Make sure to customize your resume to highlight relevant experience in maintenance management, particularly in high-tech, automated GMP manufacturing facilities. Emphasize your leadership skills and any specific achievements related to mechanical systems and non-electrical energy systems.
Craft a Compelling Cover Letter: Write a cover letter that reflects your passion for exploration and discovery, as mentioned in the job description. Discuss how your background aligns with the responsibilities of managing daily operations and leading a maintenance team, and express your commitment to compliance with GMP standards.
Highlight Relevant Experience: In your application, be sure to detail your experience with CMMS, especially One Maximo, and your familiarity with regulatory frameworks like GMP, health and safety, and environmental standards. This will demonstrate your capability to manage maintenance operations effectively.
Showcase Soft Skills: Don't forget to mention your communication and interpersonal skills, as well as your ability to foster a collaborative work environment. These soft skills are crucial for leading a high-performance maintenance team and contributing to continuous improvement initiatives.
Wie du dich auf ein Vorstellungsgespräch bei Thermo Fisher Scientific Inc. vorbereitest
✨Understand the Role and Responsibilities
Make sure you have a clear understanding of the Manager, Maintenance and Utilities role. Familiarize yourself with the specific mechanical systems and non-electrical energy systems mentioned in the job description, such as boilers and clean steam. This will help you demonstrate your knowledge and show that you're prepared for the responsibilities.
✨Showcase Your Leadership Skills
Since this position involves leading and mentoring a maintenance team, be ready to discuss your leadership style and past experiences. Prepare examples of how you've successfully developed high-performance teams and fostered a collaborative work environment.
✨Highlight Your Compliance Knowledge
Regulatory compliance is crucial in this role. Be prepared to talk about your experience with GMP standards and any relevant regulatory frameworks. Discuss how you've ensured compliance in previous positions and how you would approach audits and inspections.
✨Demonstrate Problem-Solving Abilities
The job requires efficient problem-solving skills, especially in a high-tech, automated environment. Prepare to share specific examples of challenges you've faced in maintenance management and how you resolved them. Highlight your analytical thinking and any process improvement initiatives you've led.